제조업에서의 고무 가공 종류와 적절한 가공 방법 그리고 고무의 종류
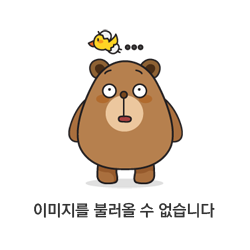
일용품과 공산품 등 폭넓게 사용하고
갖은 업계의 제조를 지탱하는 고무 제품.
정밀한 고무 가공을 하려면 사용 용도 및 재질에 대한
적절한 지식과 가공 기술이 요구됩니다.
이번 포스팅에서는 고무 가공에서 실패하지 않기 때문에
알아야 할 일에 대해서 설명하고자 합니다.
고무 가공품은 다양한 용도에 이용된다
고무를 사용한 제품과 부품은 일반 가정에서 쓰는 일용품과 전자 제품은 물론
자동차 공업용 기계 등 폭넓게 이용되고 있습니다.
사용 용도는 다양하지만 주로 미끄럼, 약품과 액체의 유출 방지,
금속끼리의 상처 예방 등에 이용되는 경우가 많습니다.
고무, 완충재, 실 자재 등이 대표적입니다.
국내의 고무 제품의 수요는 시대와 함께 변화했으며 과거에는 자동차,
공업 기계 등 부품 가공이 메인이었지만,
최근에는 반도체 등의 제조 장치 및 의료 기기 수요가 높아지고 있습니다.
고무의 종류와 특징과 주요 사용 용도
고무의 종류와 특징에 의해서, 잘하는 환경이나 용도가 다릅니다.
그래서 고무 가공에서 실패하지 않으려면 사용 용도 및 역할에 맞는
적절한 고무를 선택하는 것이 중요합니다.
고무의 종류와 그 특징, 일반적인 사용 용도를 설명 드리겠습니다.
천연 고무(NR) | 반발 탄성, 기계적 강도 인열 강력 강도가 뛰어난 반면 내유성, 내열성이 떨어진다. | 트럭의 타이어 호스, 구두창. 일반 공업 용품 등 | -30〜65℃ | 60° |
니트릴 고무(NBR) | 내유성에 가장 뛰어나고 내마모성, 내 노화성도 양호. | 가스킷 오일 실 인쇄 롤·내유 호스 등 | -30〜80℃ | 70°(표준 경도)/50°/90° |
에틸렌 프로필렌 고무(EPDM) | 내후성, 내오존성, 내약품성에 뛰어나고 내한·내열성도 양호. | 자동차용 부품, 창틀 고무 스팀 호스 전선 피복 등 | 0〜100℃ | 70°(표준 경도)/50°/90° |
클로로프렌 고무(CR) | 내후성, 내오존성, 내마모성 등 평균한 성능을 가진다. | 전선 피복식 컨베이어 벨트, 고무 롤 등 | 0〜70℃ | 60°(표준 경도)/45°/90° |
부틸 고무(IIR) | 내 가스 투과성 유우.내후성, 내오존성이 좋아 극성 용제에 대한 내성 양호. | 자동차 및 자전거의 타이어 튜우브 등 | 0〜100℃ | 60° |
실리콘 고무(SI) | 반발 탄성이 고도의 내열성, 내한성을 가진다.내유성도 양호. | 가전 제품, 자동차 관련 부품·의료 기기·식품 관련 부품·절연 부품·주사제 용기 등 | -30〜150℃ | 50°/70°/30° |
불소 고무(FKM) | 최고의 내열성, 내약품성, 내유성이 있다. | 화학 공장의 내식 패킹 개스킷 다이어프램 호스 펌프 부품 등 | 0〜200℃ | 80°(표준 경도)/60°/50° |
스티렌, 부타디엔(SBR) | 천연 고무(NR)보다 내마모성 유우.기계적 특성은 좋지만, 내열성이 떨어진다. | 타이어, 호스, 구두창. 일반 공업 용품 등 | 0〜70℃ | 65° |
우레탄 고무(U) | 폴리에스테르계 폴리 에테르계가며 기계적 강도가 강하다. | 로라 타이어 벨트, 호스 쿠션 재료·제트 코스터의 바퀴 등 | 0〜70℃ | 90°(표준 경도)/80°/70°/60°/50°/30° |
고무 가공의 주요 방법 9개와 특징
고무는 금속보다 부드러운 신축성과 탄성이 있어
가공이 되기 어렵다고 생각되기 십상인 소재입니다.
그러나 재질에 의한 적절한 가공 방법을 선택함으로써
단순한 것부터 복잡한 형상인 것까지 형태로 할 수 있습니다.
고무 가공 방법은 고무의 종류에 따라서도 달라지는 건 없어
제품과 부품의 형상에 의하여 결정됩니다.
고무 가공에서 수요가 높은 9개의 가공 방법과 그 특징을 소개합니다.
①금형 성형
고무 제품의 제조 방법으로 가장 중요한 제조 법입니다.
프레스 성형, 사출 성형, 압출 성형이 있고 형상이나 생산 수량 등에 의한 선택됩니다.
큰 무더기의 생산에 적합하며, 고 정밀의 것이나 미세한 것을 제조하는 데 좋습니다.
초기 투자로 금형의 작성비가 필요하고 그 제작 납기도 걸려서,
시작과 소량 다품종 생산에는 향하지 않습니다.
참고 납기:금형 작성+제품의 제조에서 1~1.5개월
② 절삭 가공
회전 공구를 사용, 고무를 깎아 가공하는 제법입니다.
형상에 의해서 코스트나 납기는 다르지만, 1개에서 수백개 정도면
금형 성형보다 절삭 가공이 맞는 경우가 있습니다.
초기 비용(금형대)가 걸리지 않기 때문에 시제품을 만드는 데도 좋습니다.
어떤 재질의 고무에서도 가공할 수 있고 경도가 낮을수록 가공의 난이도가 올라갑니다.
"고무 가공 이라고하면 금형 성형의 이미지가 강합니다만,
깎고 가공할 수도 있습니다.
소량 다품종의 경우는 절삭 가공 쪽이 비용 절감이나 납기 단축이 되는 것이 많습니다.
또 제품의 가공 데이터는 보존할 수 있으므로 절삭 가공의 경우에도
전회의 가공 데이터를 활용한 반복 대응도 가능합니다"
참고 납기:7,14일
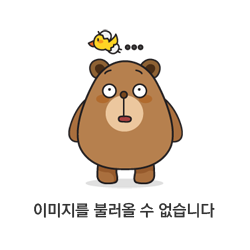
③ 톰슨 가공
나무 판자에 칼을 박은 "톰슨형"※이라는 기계를 쓰고
재료를 압박하고 꿰뚫는 가공 방법입니다.
톰슨형의 제작비는 저렴편이기 때문에 이니셜 코스트도 억제할 수 있어,
스플릿 제품 양산에 최적입니다.
재질은 한정되지 않습니다만, 판 두께 3mm이하의 것을 가공하는 데 적합하고,
3mm를 넘으면 단면의 퀄리티가 떨어질 가능성이 있습니다.
사이즈 작은 것이나 겔의 같은 부드러움의 소재를 가공하는 경우는 난이도가 높아집니다.
※지역에 따라서는 "무형"이라고도 불립니다.
참고 납기:톰슨형 작성 1,2일+제품의 제조에서 4~5일
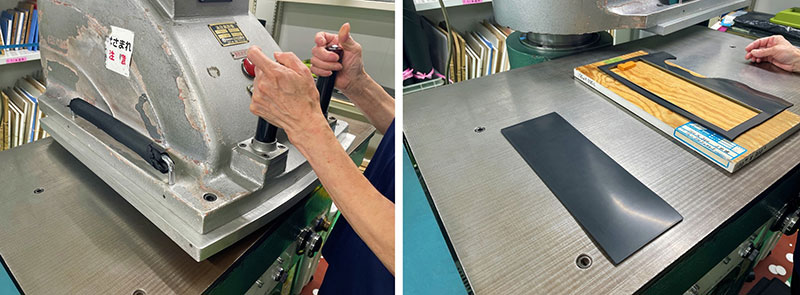
④ 커팅 플로터 가공
CAD데이터대로 칼을 움직이는 것에서 고무 시트를 자르는 가공 방법입니다.
커터와 같은 칼날로 가공을 하기 위해서 절단면의 마무리는 좋지만
칼 자체에 중후(폭)이 있어서 급한 곡선의 한 형태 등에는 적합하지 않습니다.
판 두께 5mm이하의 고무 시트를 가공할 때 적합하고,
판 두께 6mm를 넘는다면, 워터 제트 가공(아래 참조)을 선택합니다.
가공 데이터를 보관할 수 있기 때문에 반복과 같은 조건의 형상 가공이나 초등 로트에도 대응 가능합니다.
참고 납기:3~5일

⑤ 왕복 커터 가공
④의 커팅 플로터 가공과 마찬가지로 시트를 절단하는 가공 방법이지만,
칼이 수평 방향만 아니라 수직 방향으로 고속 이동하면서 움직이기 때문에
커팅 플로터 가공에서는 가공할 수 없는 두껍고 딱딱한 재료의 가공에 적합합니다.
참고 납기:3~5일
⑥ 워터 제트 가공
고압에서 분사한 물로 고무를 절단하는 가공 방법입니다.
6mm, 50mm정도 두께가 있는 제품의 초등 로트 생산을 향합니다.
미세한 가공에도 적합하기 때문에 형상에 따라서는
2~3mm정도도 워터 제트 가공을 선택하는 경우도 있습니다.
같은 절단 가공인 ④의 커팅 플로터 가공이나 ⑤의 왕복 커터 가공과 비교하면 가공 단가는 높아집니다.
참고 납기:5~6일
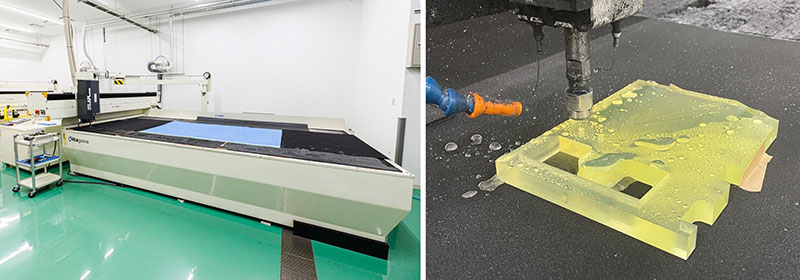
⑦ 주형 성형
"주형=진공 주형"이 일반적으로 진공 중에서 틀에
액체상의 고무를 붓고 고화시키고 성형하는 가공 방법입니다.
고무 재질은 실리콘과 우레탄에 한정됩니다.
형은 실리콘의 경우는 아크릴 제품, 우레탄의 경우는 실리콘제가 됩니다.
형의 내구성이 높은 없어 여러개~20개 정도의 단발적인 제조에서 장점이 나옵니다.
우레탄의 경우는 같은 우레탄 재료로 간이형을 만드는 제조 법이 따로 있고
형태 비(이니셜 코스트)를 줄일 수 있는데 이 방법으로 제조할 수 있는 기업은 국내에서도 극소수입니다.
참고 납기:15~20일
⑧ 인화 가공
금속 샤프트와 부재에 생고무를 가황 접착하는 가공 방법입니다.
우레탄 고무의 경우는, 틀에 액상 우레탄 재료를 붓고
열을 올려서 경화시키는 제조법입니다.
접착제에서 접착과 비교하고 접착 강도가 뛰어나기 때문에
인쇄 롤러나 후송용 롤러, 바퀴 등의 제조에 이용되고 있습니다.
참고 납기:10~15일
⑨ 연마 가공
절삭 가공 후의 고무의 표면을 더 조금씩 숫돌 등으로 깎고
매끄러운 상태로 하기 위한 가공 방법입니다.
다른 가공 방법으로 잘랐을 때에 생긴 차이 등을 기계를 사용해서
미세 조정하고 마지막으로 제품의 치수 정밀도를 높입니다.
재질이나 경도, 제품의 부분에 의해서 연마되지 않는 것도 있기 때문에
외관과 기능적으로 연마가 필요한 곳만 가공합니다.
납기:마무리로 하기 때문에 각 공정 속에 포함됩니다.
일반적인 고무 가공의 5개 공정
고무 제품을 완성하려면 어떠한 공정을 거쳐야 할까요?
일반적인 고무 가공의 5개의 공정을 소개합니다.
① 재단
도면상의 치수와 형상을 확인하고 재료의 절단여유를 남기고 절단합니다.
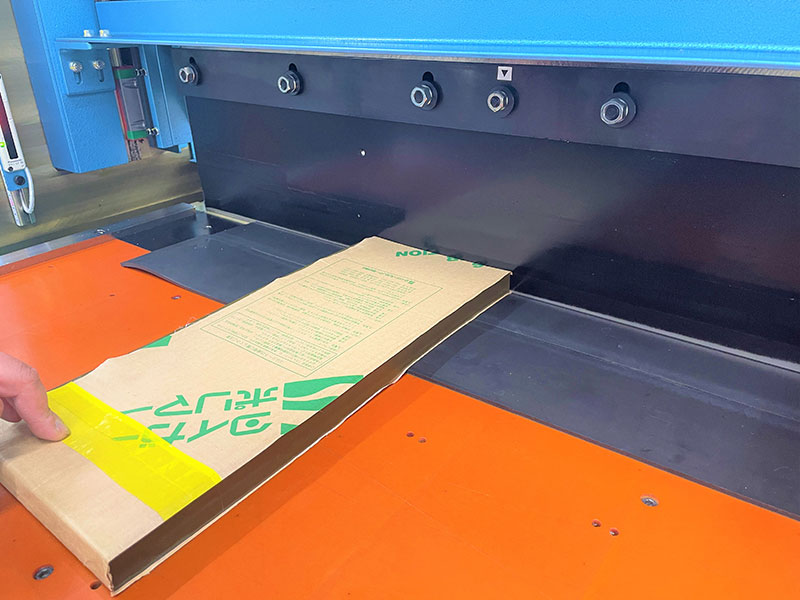
② 가공 전 공정(가공 준비)
도면 확인과 가공의 절차, 가공 설비 사용 등을 실시합니다.
③ 가공 작업
절단 및 절삭, 연삭을 갖고 도면이나 의뢰서의 치수와 형상에 가공합니다.
④ 마무리
가공품에 부착되어 있는 오염이나 윤활유 등을 용제를 사용하고 탈지·세정합니다.
⑤ 검사
지정의 치수와 형상이 되고 있는지, 노기스나 화상 측정기, 스캐너 등에서 검품합니다.
2021.12.01 - 표면 처리의 종류와 특징 처리 방법, 용도, 적절한 재질에 대해 해설
2022.06.13 - 플라스틱의 열화 원인과 플라스틱 수명 예측의 실험 방법을 소개한다.
플라스틱의 열화 원인과 플라스틱 수명 예측의 실험 방법을 소개한다.
플라스틱의 열화 원인과 플라스틱 수명 예측의 실험 방법을 소개한다. 플라스틱 성형품은 원료가 되는 합성 수지의 종류에 의해서 악화 요인이 다릅니다. 시험 검토가 진행되면
kanonxkanon.tistory.com
2021.09.07 - NAK55의 특징, 성격, 성분, 처리, 가공 방법 정리
2021.12.20 - 금속 성질 / 황동의 특징, 장점, 단점, 성질 설명한다
-
'소재 및 가공기술 > 금속 성질' 카테고리의 다른 글
A7075(초 두랄루민)이란? 특징과 유사 소재의 차이를 설명한다 (0) | 2023.02.24 |
---|---|
구리 및 구리 합금의 종류, 특징, 용도에 대해서 알아보자 (0) | 2022.12.23 |
제조에 필수적인 철강은 어떤 것일까? 철강 재료의 주요 특징과 종류 (0) | 2022.12.15 |
신소재 열가소성 엘라스토머(Thermo Plastic Elastomer, TPE)의 물성과 종류 (0) | 2022.11.23 |
은 합금의 종류 및 은 합금의 조성이나 녹는점, 경도, 특징에 대해서 (0) | 2022.11.19 |
댓글
KaNonx카논님의
글이 좋았다면 응원을 보내주세요!
이 글이 도움이 됐다면, 응원 댓글을 써보세요. 블로거에게 지급되는 응원금은 새로운 창작의 큰 힘이 됩니다.
응원 댓글은 만 14세 이상 카카오계정 이용자라면 누구나 편하게 작성, 결제할 수 있습니다.
글 본문, 댓글 목록 등을 통해 응원한 팬과 응원 댓글, 응원금을 강조해 보여줍니다.
응원금은 앱에서는 인앱결제, 웹에서는 카카오페이 및 신용카드로 결제할 수 있습니다.